May Supply Chain Update
Two months ago, as we published our March update, Russia had invaded Ukraine. The geopolitical tensions related to this war are intensifying. The war’s impact on our economy thus far is largely inflationary as we absorb increases in cost for energy, food and other products. The impact on our industry’s supply chain has been limited, but the tensions of the war are felt in our businesses.
Greg Ip, in his April 28th Capital Account update in The Wall Street Journal, chronicles the rise in inflation we are experiencing, compounded by Russia’s invasion. He shared that: “the decades preceding the pandemic were characterized by chronically weak demand and a seemingly limitless supply of capital, labor, and raw materials, resulting in a persistently low inflation and interest rates. Those conditions have since flipped. Demand is robust, especially in the U.S. where fiscal and monetary support have been especially generous. Advanced economies report shortages of labor, and Covid-19 continues to snarl supply chains, most recently in China”. Click HERE to peruse Mr. Ip’s full article.
Mr. Ip represents that over time, supply chains will adapt to the short-term imbalance in demand/supply like we have experienced since the pandemic. For example, will the steep increase in treasuries and mortgage rates eventually dampen demand due to this impact on affordability? From a historical perspective, is a 5% interest rate realistic – have the rates we’ve enjoyed the last two years, while healthy for our industry’s growth, been too low?
Interestingly, we are experiencing lead time improvements for many product lines. To be clear, these lead times are not close to “normal” as we would have defined them pre-pandemic. For example, vinyl window lead times of less than 10 weeks are dramatically lower than the 20+ weeks we experienced much of last year. We’ve together adapted our build/supply prices around these extended but improving lead times. See below for a detailed review of lead times by product line.

Demand for products continues to be strong due in part to the considerable backlog of permitted versus completed jobs (see chart to the left). The Department of Labor reported that privately owned housing units authorized by building permits in March were at a seasonally adjusted annual rate of 1,873,000. This is 0.4 percent above the revised February rate of 1,865,000 and is 6.7 percent above the March 2021 rate of 1,755,000. Note that the completion trend continues to track well behind new starts, so there is a considerable backlog of work.
Industry economists report that builders continue to experience good demand due to the combination of limited existing home inventory (see Housing Supply chart below) and a desire to lock in mortgage rates with the continuing upward rate trend (see Freddie Mac chart below).
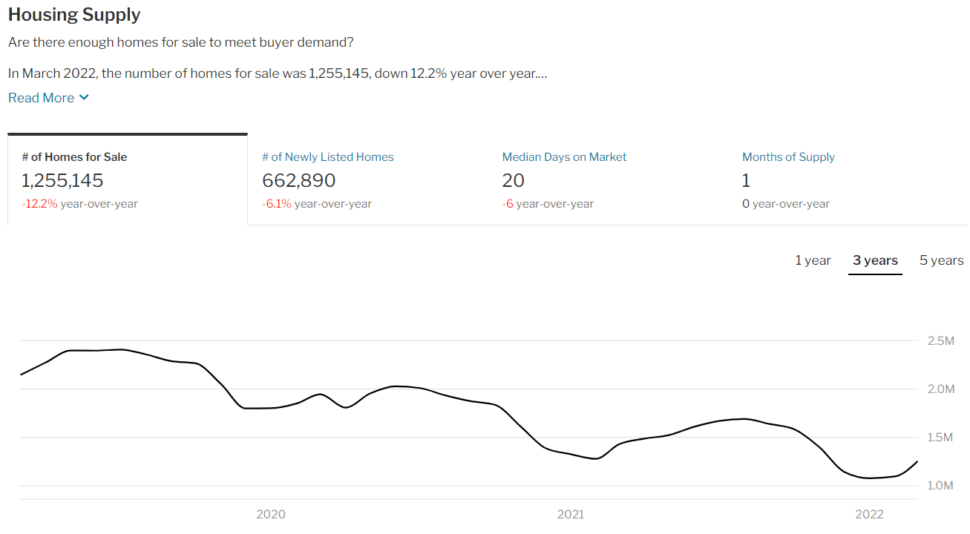
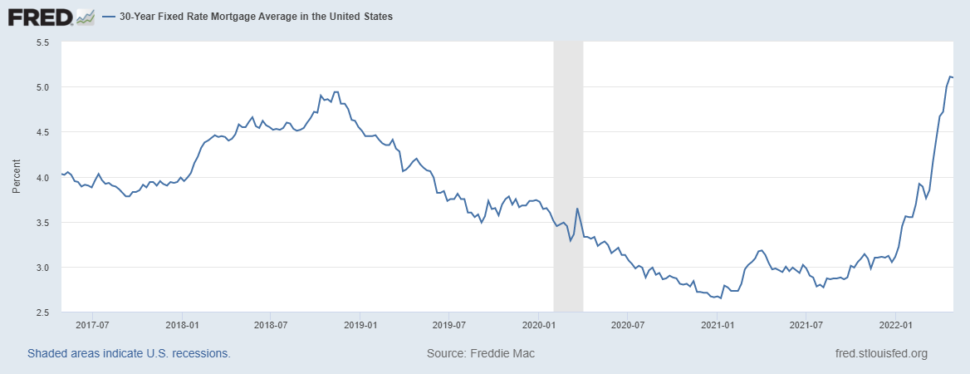
Lumber and panel prices were highly volatile in April. When we published our April update, lumber prices had peaked and were beginning a steep fall. Over the last two weeks, pricing has modestly increased, likely related to the demand referenced above. Our suppliers have shared that this inflection point has strengthened demand, as buyers had paused due to the steep decline.
Panel prices (reflected in OSB chart below) declined smartly in April. Note that panel price declines lagged lumber in 2021 too, when they also declined quickly. You’ll see that OSB prices were down modestly last week and printed up 5% as we close April.
Also note that price levels for lumber and panels at the new inflection points are higher than the similar inflection points experienced in 2021. This may be due to the strength of the overall housing industry.
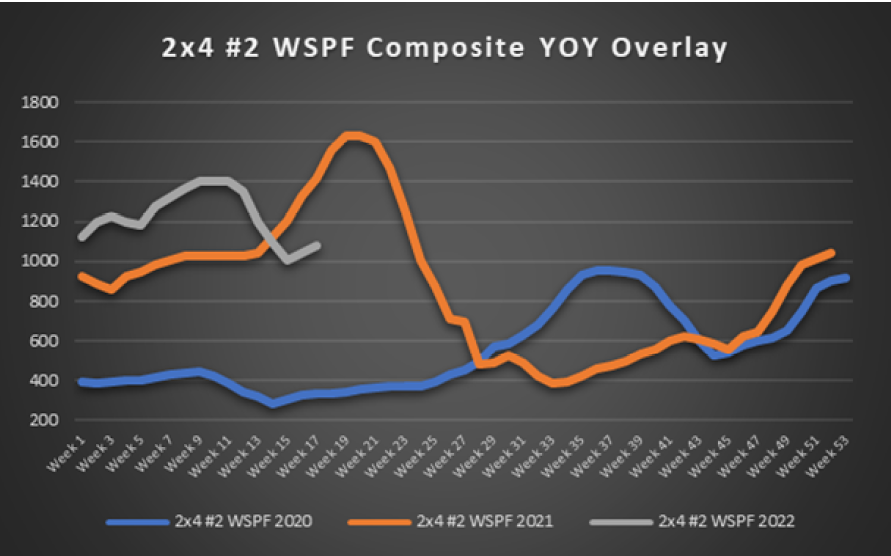
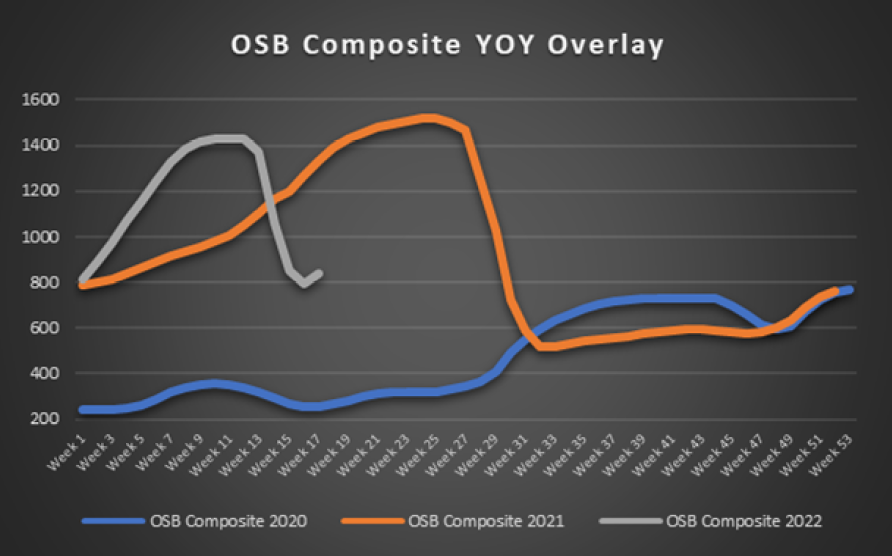
In our product line update below, you’ll see that pricing continues to push higher due largely to higher raw material, labor and distribution costs. Certainly, strong demand is also a factor. A few are worth highlighting:
- Pricing for exterior doors has increased by 6-20% due to reasons shared above.
- Lead times for aluminum clad windows are 22 weeks to over a year.
- EPDM rubber roofing is on allocation and fasteners to apply these products are limited in supply.
- EWP lead times are extended to 4+ weeks and prices continue to rise. See additional details below.
It will be interesting to see when we experience some moderation and/or decline in prices for products other than lumber/panels, should Mr. Ip’s historical logic about a supply chain rebalance play out.
Regards, Bob Wood, President
P: 717-792-2500 | E: [email protected]
CABINETS:
- Gallery lead times are currently 6-12 weeks.
- Omega / Dynasty lead times are currently 8-12 weeks for framed and inset cabinetry. Full access cabinetry lead times are 18-22 weeks.
- Legacy lead times are 8-9 weeks.
- Timberlake lead times are 8-12 weeks.
- Quality Cabinets lead times are 9-10 weeks.
- Aristokraft lead times are 12-14 weeks.
- WOLF Cabinetry lead times are 6-8 weeks.
FLOORING:
- Mohawk has announced a price increase of 5% effective May 9th.
- Shaw has announced a price increase of 8% on residential, commercial, Mainstreet carpets, and cushion.
DECKING:
- Trex has announced a price increase of 8% on Select Decking and on Signature Railing effective on May 1st.
WINDOWS & DOORS:
- Andersen Windows and Doors lead times on 100 Series are 7-16 weeks, 200 Series are 4-11 weeks, 400 Series are 7-16 weeks, A-Series are 11-20 weeks, E-Series are 66-67 weeks, MultiGlide are 42-43 weeks, and folding doors are 24-25 weeks. Most window and patio door screens are 14-15 weeks.
- Marvin Windows and Doors lead times on the Elevate Collection is 16-19 weeks, Essential Collection is 18-20 weeks, and Signature Collection is 19-27 weeks.
- Ply Gem lead times have improved, but are still extended. 1500 Series Single Hung is 8 weeks, and the Pro Classic Double Hung is 3 weeks.
- Simonton’s lead time is 2-3 weeks on the new construction series and 2 weeks on the replacement series.
- Silver Line lead time is 3 weeks on single hung and 2 weeks on double hung.
- Atrium lead time is 11 weeks on new construction double hung, 13 weeks on new construction single hung 150/160 Series, and 17 weeks on SH 130 Series.
- 7-D Windows lead time continues to be 3-4 weeks. Tempered glass units are 12-16 weeks. Contact your sales rep should these lead times enable you to achieve a quick turn project.
- MI Doors has announced the following price increases effective May 1st:
- Interior doors – 20%
- Exterior doors – 25%
- Aluminum & steel commercial doors & frames – 15%
- Millwork, pre-hanging/machining & pocket frames – 17%
- Reeb has announced the following price increases taking effect July 1st:
- Exterior fiberglass and steel doors units – 11-14.5%
- RSP steel fire doors – 6%
- Hollow core doors – 6-14%
- Solid core doors – 8-10%
- Flush doors – 6-20%
- 90 minute hollow metal – 8%
- BenBilt has announced a price increase of 14.5-16% on all Therma-Tru products effective on June 10th.
EXTERIOR TRIM:
- Versatex has announced a price increase of 7% effective on May 2nd.
- Reeb has announced a 7% price increase on all Fypon products effective on July 1st.
- Mid-America has announced a price increase of 6-9% on shutters, blocks and vents effective May 14th.
GARAGE DOORS:
- Lead times are 2-19 weeks depending on style and color selection.
INSULATION:
- Insulation continues to be on allocation and supply issues will more than likely continue through this year.
ROOFING:
- EPDM rubber roofing and accessories have extended lead times and are on allocation. They have announced a price increase on membranes of 6-10% and up to 25% on termination bars, adhesives, cleaners, and fastening products.
- Central State Roofing has been experiencing shortages in metal products & extended lead times on some orders. Check with your rep for current lead times.
SIDING:
- Berger continues to have extended lead times on all coil stock, flashing & roof edge, ranging from 45 to 120 days.
- CertainTeed has returned all suspended vinyl colors back into the market. Myers is currently taking orders for May 19 deliveries.
- James Hardie has announced that all shingle siding is on allocation. They have also announced a price increase effective June 20th.
- Lomanco has announced a price increase of 6% on all aluminum products effective on May 16th.
CAULKING & ADHESIVE:
- Caulking continues to be hard to locate. The lack of raw materials needed to manufacture caulking has put a strain on the supply chain. Myers is doing everything it can to secure caulking.
- Construction adhesive has been affected by the same constraints as caulking, only worse. One of our main suppliers is not manufacturing adhesive basically because of the lack of raw materials needed for production. Myers has added a new construction adhesive TYTAN Foam. Click HERE to learn more about TYTAN.
GYPSUM:
- Drywall and accessories will have a price increase of 8-15% effective on May 1st.
EWP:
- LP is experiencing extended lead times of 4 plus weeks with limited supply on-hand. They have announced the following price increases effective May 2nd:
- I-Joists: 17-24%
- LVL: 5-8%
- Rim Boards: 15-18%