July Supply Chain Update
Last month, our update was presented around the theme of “The War on Inflation”. In June, the war waged on. On June 15 the Fed increased the fed funds rate by .75%. While consistent with their open dialog about raising rates to fight inflation, the financial markets declined smartly in early June. Since then, financial markets have been volatile as investors seek to discern when the Fed’s actions may begin to reverse the trend of heightened inflation. Analysts seek daily to assess the impact of the Fed’s actions on consumer behavior, which ultimately impacts the economy and corporate earnings for all industries. Other critical factors on the financial markets include the impact of potential covid strains, the war in Ukraine and the Fed’s handling of monetary policy. Click HERE to read U.S. Bank’s June 22nd article.
What indicators might we consider in June that depict the inflationary impact of the economy on our industry. Analysts report that builders are experiencing softer lead activity and increased cancellations. Redfin reported that “homes for sale” searches on Google were down 14% from the prior year and their Homebuilder Demand Index (a measure of requests for tours and other services) was down 16% (new and existing homes combined). Mortgage purchase applications were down 10% from a year earlier, while they increased slightly from levels in earlier June.
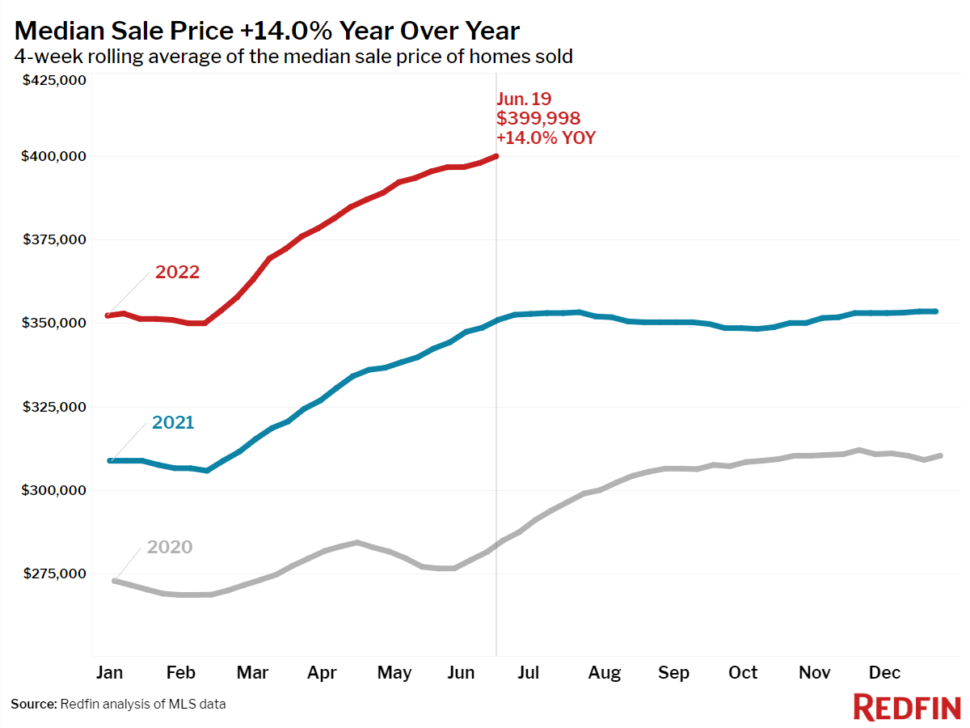
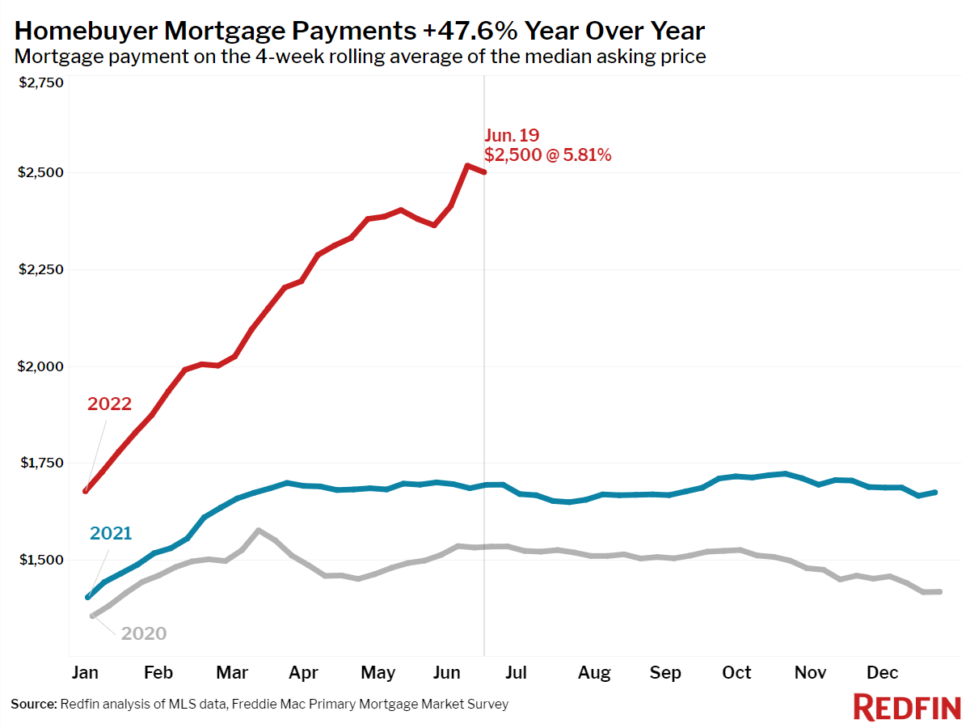
The charts above reflect the impacts of inflation and increased mortgage rates for the home buyer. Medium sales prices are up 14% over 2021 (new home prices are estimated to be up approximately 20%). When combined with the increase in mortgage rates to 5.8% in 2022 (an increase of .7% in June alone), homeowner mortgage payments are up close to 50% in 2022. While 5-6% mortgage rates are reasonable historically, this impact in one year is significant.
Are inflationary pressures softening in our industry? As we’ll discuss below, pricing for lumber and panels dropped materially in the last 60 days. While we have yet to see any price erosion for fasteners and hardware, scrap metal prices are declining. The timing or cadence of price increases seems to be slowing. The level of price increases being announced are also somewhat lower in the aggregate than trends we experienced months ago.
On June 27, Will Parker wrote in the Wall Street Journal that “Bidding wars have long been a staple of hot housing markets, where buyers compete with offers above the seller’s listing price. Now, these contests are becoming more commonplace in the rental market. Real-estate agents from New York to Chicago and Atlanta say they see more people than ever making offers above asking to lease homes and apartments that they will never own.” Since buyers can’t qualify for homes due to the increases described above, they face a higher rental market in some geographies. Higher rents may also drive future MF development, especially with the decline in lumber prices. An answer to the question posed to open the prior paragraph: other than for lumber/panels, the data suggests not yet.
Interestingly, the NAHB reported that “After posting four consecutive monthly declines on rising mortgage rates and worsening affordability conditions, new home sales posted a solid gain in May as some buyers rushed into the market in advance of the Federal Reserve’s June interest rate hike. Sales of newly built, single-family homes in May increased 10.7% to a 696,000 seasonally adjusted annual rate from an upwardly revised reading in April, according to newly released data by the U.S. Department of Housing and Urban Development and the U.S. Census Bureau.” As we shared in prior updates, some of the uptick in home construction is related to the backlog of permitted versus completed units. It will be interesting to learn of the June results. While stymied by inflation, the economy remains strong. Housing demand persists, while it is understandably impacted by the factors described above.
As indicated in the charts shared below, lumber composite prices continued to retreat through mid-June, then increased slightly the last 3 weeks. Analysts report that the supply chain was working down inventory levels due to the decline in pricing, so demand was weaker. It was also reported that the box stores were “silent” in the weeks when declines were steepest. With the inflection point in pricing, mills have experienced increased demand, inclusive of an uptick in product supplied for an uptick in MF interest. Transportation continues to be challenging and expensive. Early July is historically a slower supply period as some mills take down time, so capacity will decline. Note that pricing leveled off just above low levels in the summer of 2021.
Panel prices continued their steep decline throughout June. OSB is now trading at levels below the 2021 bottom, reportedly which is pushing mills closer to their break even level.
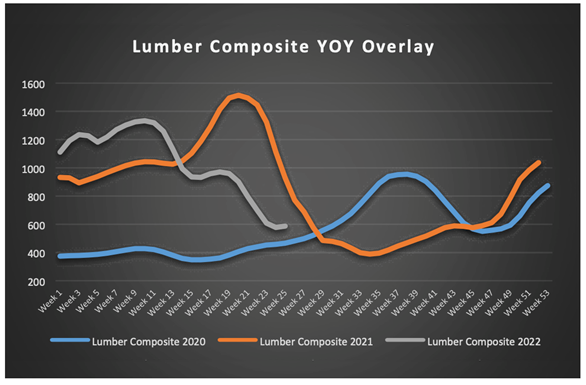
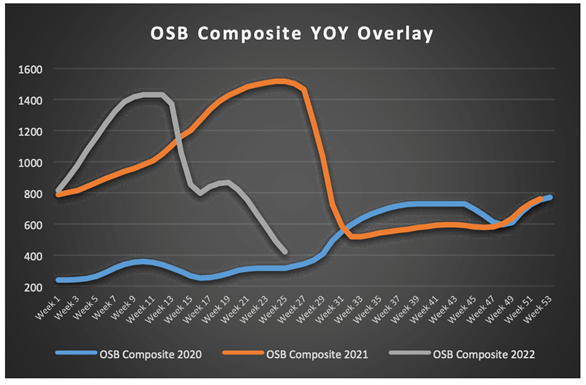
Below you’ll find our monthly update on price changes and lead times for vendors by product line that you require for your projects. As we’ve shared in prior reports, lead times are steady to improving for most product lines. Rubber roofing, caulking, some glues, pocket doors and pull downstairs have long lead times and are difficult to secure. Please engage your sales representative on your schedule, so we can assist in securing your products on time.
In conclusion, how do I process the myriad of industry leading indicators influenced by inflationary pressures? I’d volunteer that I’m confused over how and when the Feds actions will thwart inflation. I sense we are in the middle of a movie. We know the plot, but the end is yet to be written. More next month. Thanks for watching with us.
Regards, Bob Wood, President
P: 717-792-2500 | E: [email protected]
CABINETS:
- Gallery lead times are currently 6-12 weeks. They have announced a price increase of 7.5% effective July 25th.
- Omega / Dynasty lead times are currently 8-12 weeks for framed & inset cabinetry. They have announced a price increase of 5% effective July 15th.
- Legacy lead times are 8-9 weeks.
- Timberlake lead times are 8-12 weeks. They have announced a price increase of 8% effective July 1st.
- Quality Cabinets lead times are 9-10 weeks. They have announced a price increase of 8% effective July 25th.
- Aristokraft lead times are 12-14 weeks. They have announced a price increase of 7.5% effective July 1st.
- WOLF Cabinetry lead times are 6-8 weeks. They have announced a price increase of 9% effective July 25th.
WINDOWS & DOORS:
- Andersen Windows & Doors lead times on 100 Series are 3-9 weeks, 200 Series are 4-6 weeks, 400 Series are 5-16 weeks, A-Series are 11-13 weeks, E-Series are 20 weeks, MultiGlide are 20 weeks, and folding doors are 21-23 weeks.
- Marvin Windows & Doors lead times on the Elevate Collection is 18 weeks, Essential Collection is 20-21 weeks, and Signature Collection is 19-27 weeks.
- Ply Gem lead times have improved, but are still extended. 1500 Series Single Hung is 9 weeks & Pro Classic Double Hung is 3 weeks.
- Simonton’s lead time is 2-3 weeks on the new construction series and 2 weeks on the replacement series.
- Silver Line lead time is 2 weeks on single hung and 2 weeks on double hung.
- Atrium lead time is 6 weeks on new construction double hung, 10 weeks on new construction single hung 150/160 Series, and 8 weeks on SH 130 Series.
- 7-D Windows lead time continues to be 2-3 weeks. Tempered glass units are 12-16 weeks. Contact your sales rep should these lead times enable you to achieve a quick turn project.
- Reeb has announced a price increase on the following products effective July 1st:
- Fiber edge hollow core doors – 6 to 10%
- Finger-jointed edge hollow core doors – 8 to 14%
- Flush Oak and Birch doors – 18 to 20%
- Flush Lauan and Hardboard – 6 to 10%
- 90-Minute and hollow metal steel doors – 8%
- Reeb has announced the following price increases on Therma-Tru doors taking effect July 1st:
- Steel doors units – 11%
- RSP steel fire doors – 6%
- Classic Craft & Fiber Classic – 13%
- Smooth Star – 11%
- Reeb has also announced a price increase on Simpson and Woodgrain Doors effective August 1st:
- Simpson exterior doors – 8%
- Simpson interior doors – 10%
- Simpson interior door units – 2.5%
- Woodgrain interior doors – 10%
- Woodgrain interior door units – 6%
MILLWORK:
- Durawood has announced a price increase of 3% on all products effective on August 4th.
FLOORING:
- Mohawk has announced a price increase of 10% on Residential and Mainstreet Commercial Carpet styles effective on shipments on or after July 25th.
EXTERIOR TRIM:
- Reeb has announced a 7% price increase on all Fypon products effective on July 1st.
GARAGE DOORS:
- Lead times are 8-12 weeks depending on style and color selection.
INSULATION:
- Insulation continues to be on allocation and supply issues will more than likely continue through this year.
ROOFING:
- EPDM rubber roofing & accessories have extended lead times & are on allocation.
- GAF has announced a price increase of 7 to 10% on all residential roofing products effective August 1st.
- Central State Roofing has been experiencing shortages in metal products & extended lead times on some orders. Check with your rep for current lead times.
- TAMKO has announced a price increase of 7 to 10% on all residential roofing & waterproofing products effective July 25th.
SIDING:
- Berger continues to have extended lead times on all coil stock, flashing & roof edge, ranging up to 8 weeks.
- CertainTeed has returned all suspended vinyl colors back into the market. Myers is currently taking orders for July 21st deliveries.
- LP SmartSide has announced a price increase of 3-5% effective July 4th.
- Diamond Kote Building Products has announced a price increase of 3% effective July 5th.
CAULKING & ADHESIVE:
- Caulking continues to be hard to locate. The lack of raw materials needed to manufacture caulking has put a strain on the supply chain. Myers is doing everything it can to secure caulking.
- Construction adhesive has been affected by the same constraints as caulking, only worse. One of our main suppliers is not manufacturing adhesive basically because of the lack of raw materials needed for production. Myers has added a new construction adhesive TYTAN Foam. Click HERE to learn more about TYTAN.
HARDWARE:
- Simpson Strong-Tie has announced a price increase effective August 15th on Strong-Wall’s, fasteners, anchors & adhesives.